WMS (warehouse management system, Russian warehouse management system) is an information system that automates the management of business processes in warehouses — from reception and placement to storage, assembly and return.
The minimum “gentleman's” set of WMS features that any warehouse with an area of 1000-10,000 meters now has2, includes the following components.
1. Automatic identification
Product data is coded and printed on packaging and containers in the form of a label with a barcode or RFID tag; it is read using radio terminals.
2. Address storage
Each box in the warehouse is assigned its own code with its “address” (storage area, rack number, section number, shelf number, etc.), and each item is also assigned its own “address” upon receipt.
3. Optimization of composite cargo assembly processes
The program suggests the shortest route that a picker must take in order to quickly collect all goods and materials for shipment.
4. Product accounting
Inventory, dealing with marriages and returns.
Large logisticians with warehouses with an area of more than 10,000 m2 this is not enough: they need to integrate their WMS with other information systems — both internal (pipeline management system, access control system, etc.) and external (information systems for customers — merchants —
and performers — delivery services, freight forwarding companies, etc.).
Such companies already have WMS (in some cases not even one, but three or more), but the issue of “linking” with other information systems, as a rule, has not yet been resolved. How critical is it to have time to order the development of such integrations today? What benefits do logisticians miss when they put the development of complex IT solutions on the back burner?
Let's talk in more detail about the main benefits of integrating WMS with other information systems for large logistics companies.
Top 5 tasks that WMS integration with other IS solves in 2020
1. Get ahead of competitors in terms of service
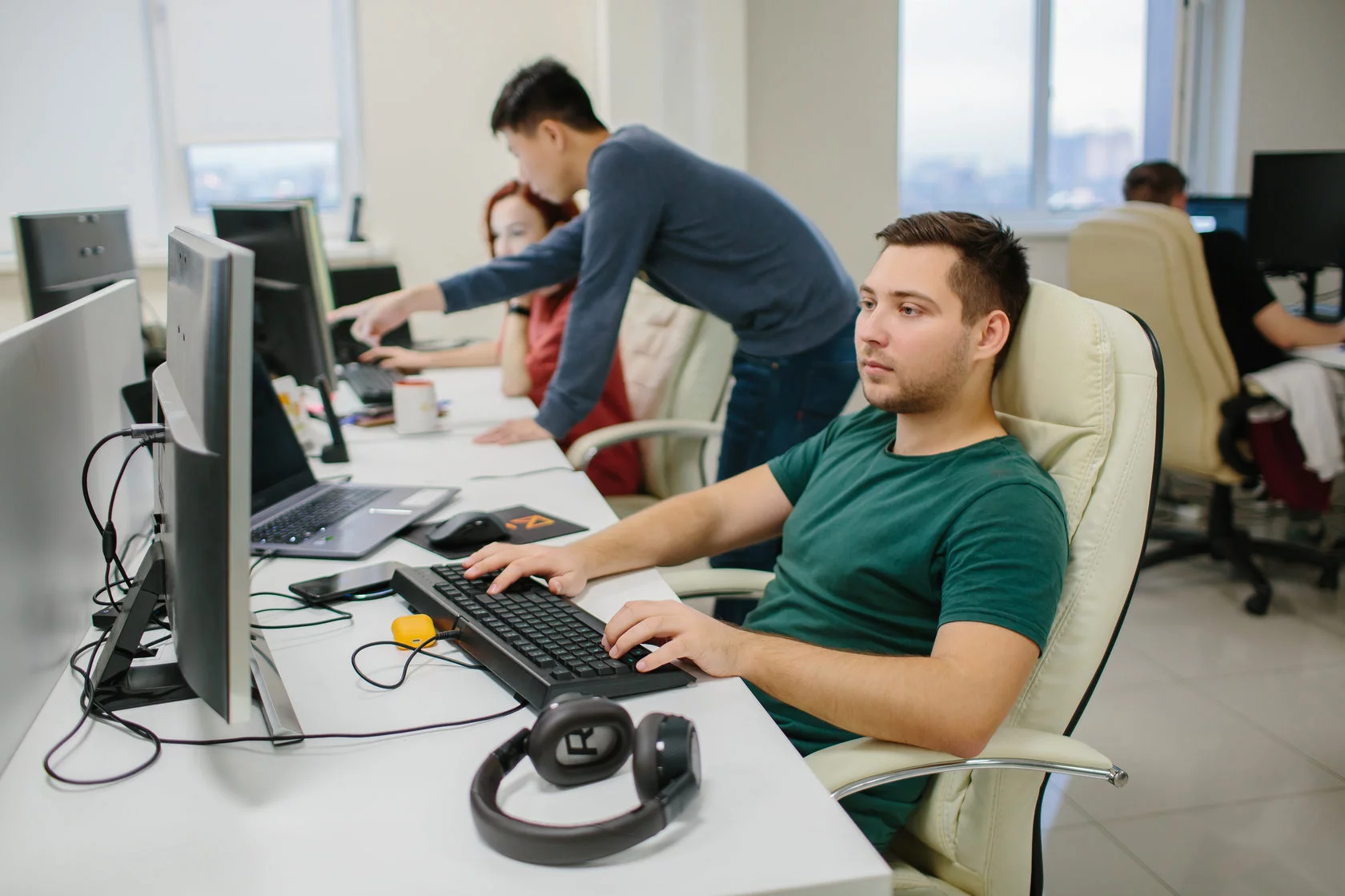
In October 2019, the Council of Supply Chain Professionals made forecasts for 2020. Experts say that the key value for many customers of transport and logistics companies will not be low prices, but a high level of service. This includes the level of introduction of IT technologies into business processes, because the speed and quality of all work depend on this.
In order to comply with these trends as much as possible and stay ahead of competitors in terms of speed and quality, it is necessary to combine all information systems into a single network. Then information about all transport and logistics operations will be processed quickly and without losses, orders will be transparent, it will be easy to form them and track their implementation. This means that such a company will be more profitable for partnership than many others.
2. Join E-commerce and become an attractive fulfillment operator
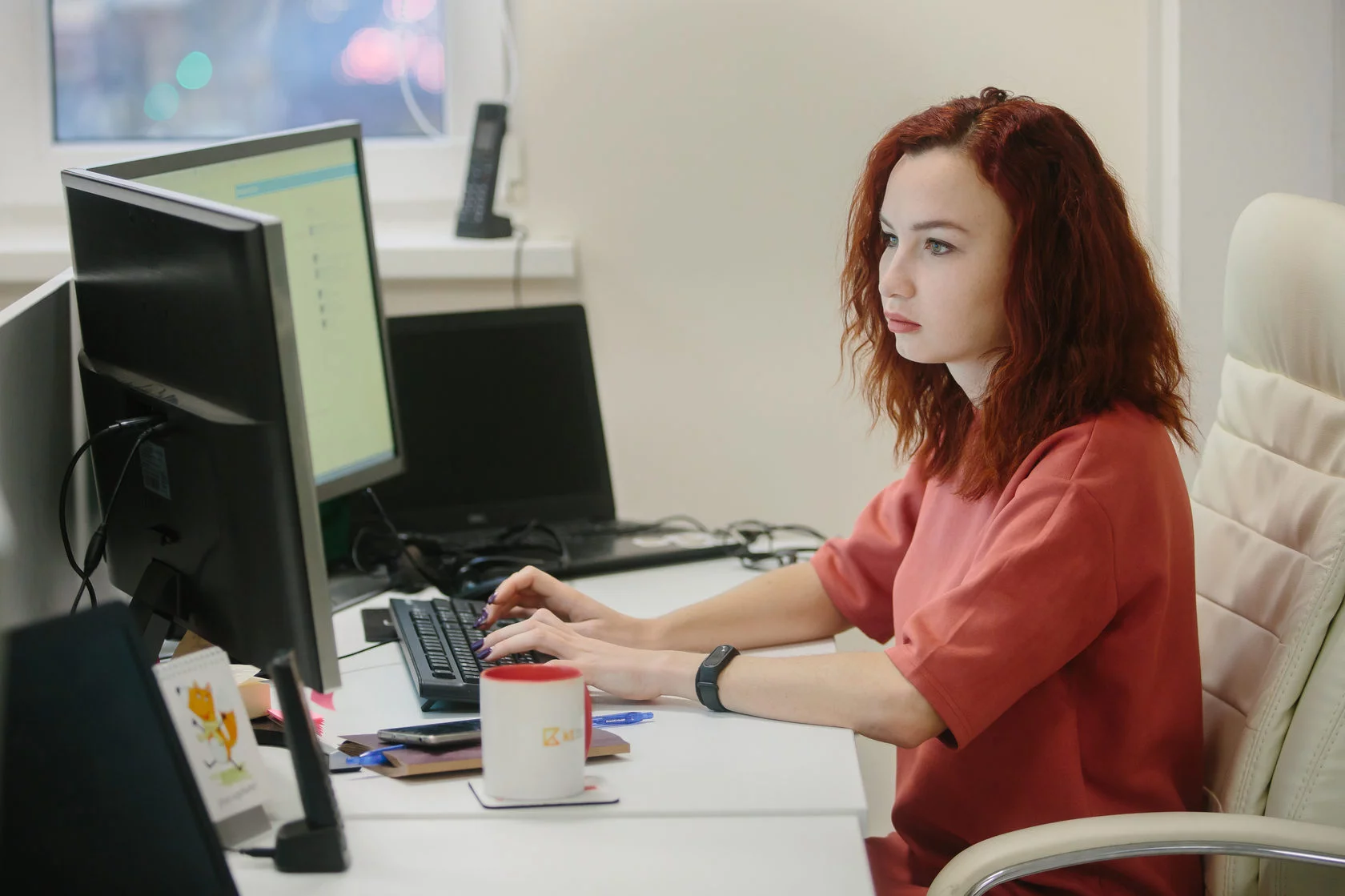
According to PricewaterhouseCoopers, digitalization is the main trend in the transport and logistics industry. Trading is increasingly going online, and e-commerce logistics has its own peculiarities (high requirements for the “last mile” service, one-time orders, fast delivery anytime and anywhere). Those who better adapt processes to these requirements will have access to a market that, in the next five years, can grow 2.5 times. Industry leaders are already integrating their WMS with delivery services, achieving a competitive advantage: they need to jump onto this train in 2020 so that it doesn't hurt excruciatingly in five years (or maybe even earlier).
What technologies should be used in development?
While the majority of logistics customers use Magento CMS, it is also convenient for logisticians to use Magento when working with them. This way they can simply duplicate orders from online stores into this system and then process them at home. The advantage of Magento is that it is specifically optimized for e-commerce. It is convenient to use it to create one external gateway through which you can receive orders from many e-commerce partners and integrate this system with your WMS once, instead of having to carry out expensive integrations each time a new merchant is connected. This significantly reduces the cost of connecting new partners to your warehouse.
Possible WMS integrations with Magento:
- integrations with product suppliers — WMS can be “tailored” to both a store and a marketplace, you can create your own marketplace and organize direct orders from a warehouse;
- LMS integrations — Magento can collect information about orders, build status and send the necessary data to the door-to-door delivery service;
- integrations with internal information systems (e.g. conveyor, sorter, etc.)
Depending on the tasks, it is possible to use the boxed version of Magento with refinement and writing modules or creating unique microservices.
3. Eliminate errors due to human error
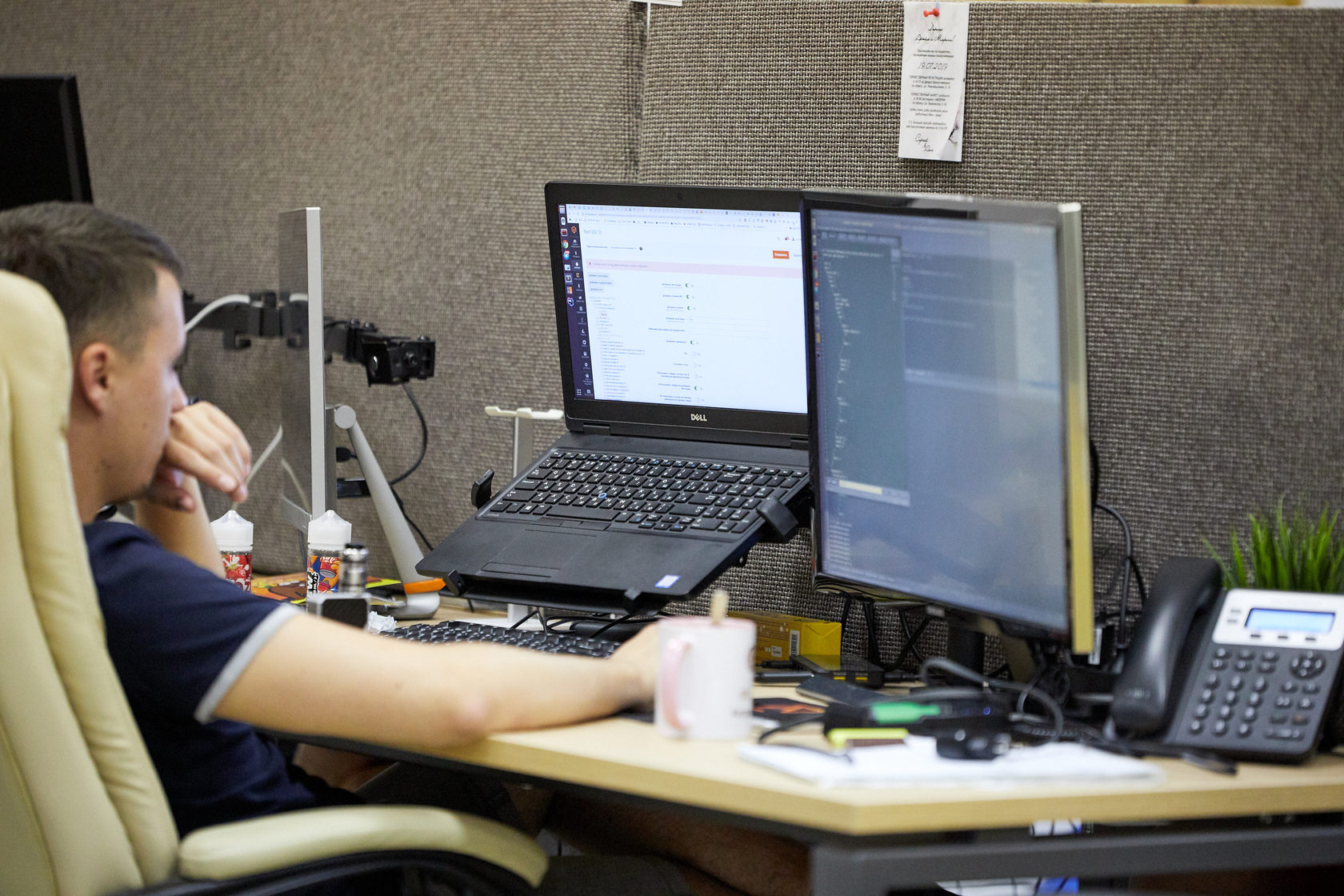
“Anything that can go wrong will go wrong.”
Murphy's Law
If you follow the Poka-yoke (“error protection”) philosophy, born at Toyota factories, you probably care about ensuring that business processes exclude the very possibility of miscalculation and oversight. This is easy to do with modern WMS: you need to properly program the equipment that employees use, or even eliminate some manual operations from the work cycle by integrating WMS with a warehouse conveyor, printing service, etc.
In such conditions, it is impossible to confuse something, lose it, forget it through carelessness.
4. Ensure the safety of goods and materials
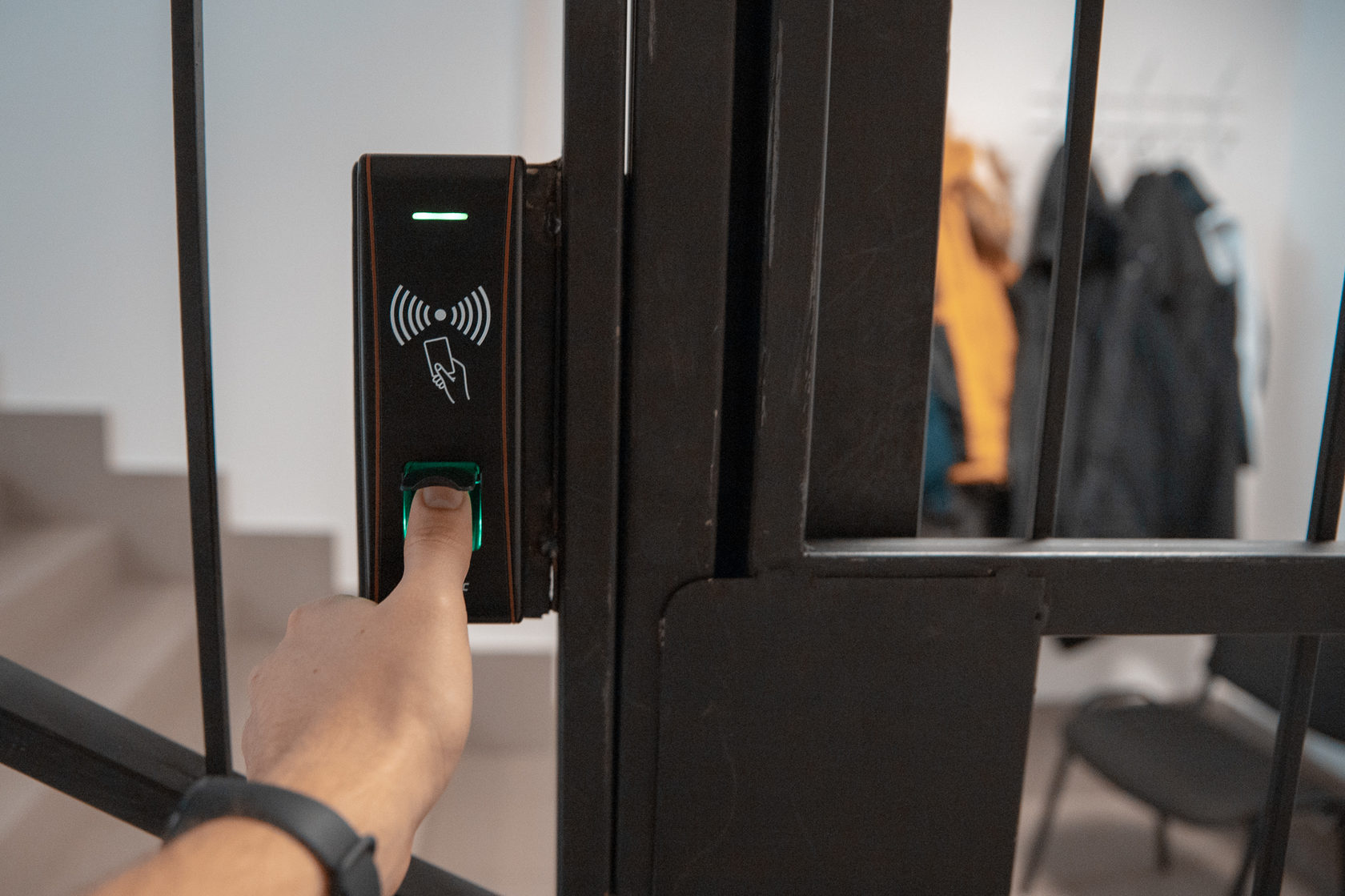
First, WMS can be integrated with access control and management systems (ACS) to record all data on the movement of employees and vehicles from and to the warehouse. Entrance/exit control can be carried out not only using electronic passes, but also using biometric data (face, fingerprint) or using video surveillance cameras. This prevents theft and helps you quickly find the culprits if a theft does occur.
Secondly, when WMS is installed in a warehouse, employees are less likely to read goods manually or not at all, thus minimizing the risk of errors or fraud when counting and inventories. Operators are “armed” with radio terminals or other barcode readers, and instead of manually counting and making mistakes on the list, they simply hold the device to the barcode. Information from the sensors of the readers is immediately sent to the inventory accounting system (if integration is configured). This makes the work faster, and most importantly, increases the reliability of the results.
5. Support internal reforms and changes in business processes
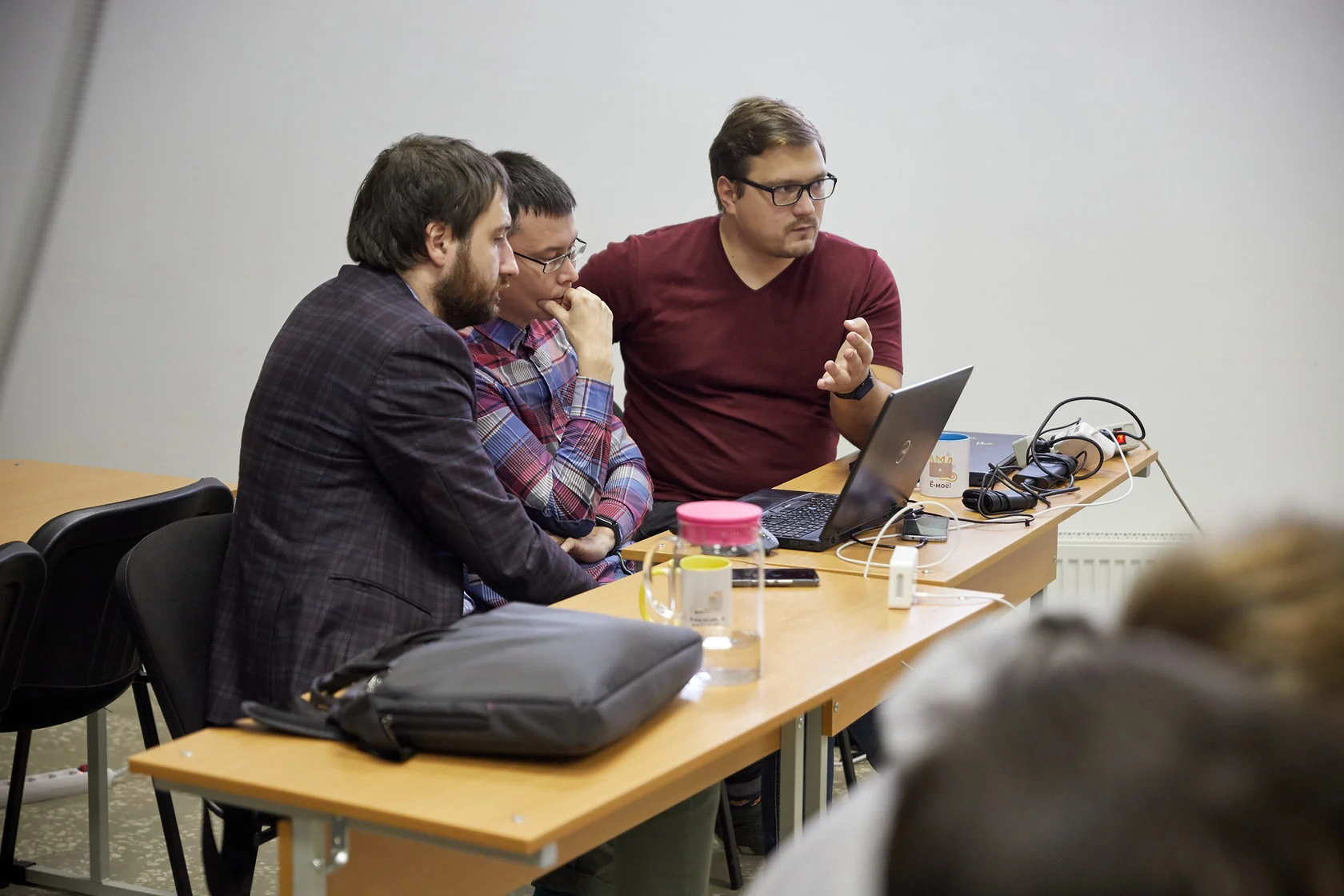
“The market offer [of carriers and freight forwarding companies] is very large, and those companies that can reduce transportation costs without inflating tariffs, but by optimizing business processes benefit, — explains expert Lyudmila Simonova, Partner at M.A.Research. “Such companies can grow by 50% per year even in a falling market: there are plenty of examples among major players.”
The success of implementing and integrating WMS largely depends on the streamlining of business processes. Sometimes company reforms begin with a review of processes, and automation is delayed later. But more often, on the contrary, starting to implement WMS and other information systems “highlights” the problem like a spotlight: it is impossible to automate chaos.
For example, how are online orders processed in warehouses without “stitching” WMS with the IS of freight forwarders?
The operator must manually send all data about orders that need to be delivered from the warehouse to the delivery service. This usually looks like an Excel file or an electronic application in the “Personal Account” on the LMS website. After that, a driver arrives to pick up the cargo with documents. There are a lot of documents, and all of them are prepared, processed and stored by hand. Can you imagine how time-consuming all these operations are in warehouses with a cargo turnover of several million SKUs daily? The system is cumbersome and unscalable, but these business processes can be successfully automated (we have extensive experience in this matter), and unnecessary operations can be eliminated.
By the way, how your IT contractor feels about BPM (business process management) says a lot about his approach to quality. Does it analyze your current processes and suggest improvements? Or is he “doing his own thing” and “sculpting from what happened”?
When working on complex system integrations, we are going in the following sequence.
1. At the first stage, we audit current solutions and optimize technological and business processes in accordance with the customer's tasks.
We do this because we care about how the client builds the process chain; everything must be strictly functional and at the same time justified in terms of their business goals. The focus is on the customer's profit from development.
2. The second stage is the actual development of the software.
This includes creating the necessary modules, subsystems, components, services, user and functional interfaces.
3. At the third stage, we prepare operational documentation.
It will help the customer start using the implemented solutions.
4. The final stage.
Training and certification of employees who will use our developments.
Read more about how we implemented the BPM system in kt.team and why we recommend it to others in our blog.
findings
We reviewed five main reasons for implementing WMS and its integration with other information systems in the warehouses of large logistics companies. It would seem that all the arguments are in favor. But let's not forget about an important condition that puts an end to half of such integrations.
We wrote about this in one of our previous articles —
”Impact Mapping, Unit Economy, and PDCA: Smart Management of E-commerce Development”.
Until the customer's team, together with the developers, conducts Impact Mapping — an analysis of whether tasks meet business goals — and calculates the unit economy of all planned decisions, we should not start integrations. We recommend that you pay special attention to this before ordering development. If you need advice on this topic, we are always ready to help.